Le TCO comportera donc 32 barrières infrarouge disposées en X avec un pas de 3cm et en Y avec un pas de 2cm. Chaque barrière est constituée d’une LED infrarouge (IR) et d’un phototransistor IR. Il n’est ni souhaitable ni possible que les 32 barrières soient alimentées simultanément.
Pas souhaitable parce que chaque LED IR va baver sur les phototransistors IR de ses voisines. Si les LED IR sont alimentées en permanence, l’interruption de faisceau ne sera pas détectable car les LED voisines illumineront le phototransistor correspondant au faisceau interrompu.
Impossible car alimenter 32 LED IR sous 5V avec, disons, 100mA demanderait 3,2A ce qui nécessite plusieurs régulateurs 5V et des complications sur la carte de pilotage du TCO.
De plus, les LED IR permettent une alimentation par impulsion avec un courant bien supérieur au courant admis pour une alimentation permanente. De cette manière on peut envoyer une impulsion lumineuse de forte intensité et différencier nettement l’impulsion reçue par le transistor de la lumière IR ambiante.
Caractéristiques des composants
La LED IR choisie est une Vishay® TSHF5210 dont voici la datasheet. Il s’agit d’une LED IR conçue pour les télécommandes et plus généralement pour la transmission de données. Ses caractéristiques dynamiques sont donc bonnes avec des temps de réponse de 30ns. Son intensité lumineuse est excellente avec 180mW/sr. Le faisceau d’émission est assez étroit : 10°, ce qui permet de ne pas trop éclairer le paysage. Les autres caractéristiques qui nous intéressent sont données à la figure 3, page 3 de la datasheet. Figure que je reproduis ci-dessous.
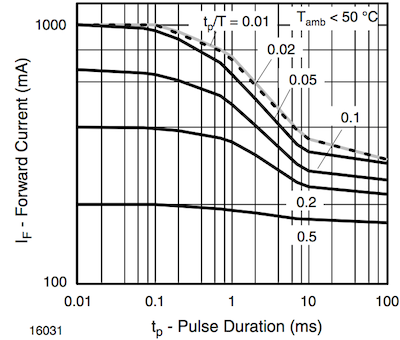
Comme on peut le voir, il est possible de monter jusqu’à 400mA avec des impulsions de 1ms pourvu que le rapport cyclique soit autour des 15%.
Le phototransistor est un L-93DP3C de KingBright dont voici la datasheet. Voyons donc expérimentalement de quoi il retourne.
Le banc d’essai
Le banc est constitué d’une baguette en pin et de deux supports pour d’un côté la LED IR et de l’autre le phototransistor IR. Afin de mettre le plus de chances du côté de Murphy, la distance entre les deux est de 74cm au lieu des 59cm que j’aurai sur le TCO. Pour la même raison, les fils qui vont de la platine d’essai au phototransistor font 1m de long.
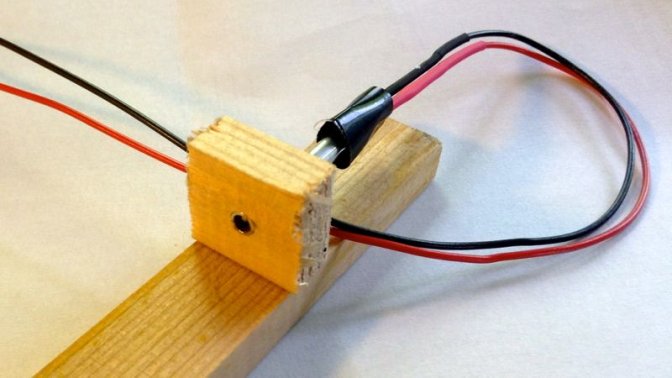
L’électronique de commande est très simple est est représentée dans le schéma ci-dessous. Lorsque le faisceau IR n’est pas interrompu, le phototransistor IR est passant et un niveau bas est mesuré. Lorsque le faisceau est interrompu, le phototransistor IR est bloqué et un niveau haut est mesuré.
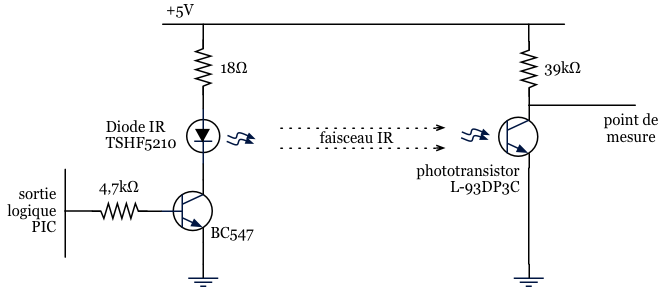
Il s’est rapidement avéré que la durée de l’impulsion avait une grande influence. En effet, le phototransistor a un temps de réaction assez long. Avec une impulsion de 200mA dans la LED IR, il faut de 700µs à 800µs pour que le signal au point de mesure descende en dessous de 1V. Le signal récupéré au point de mesure est montré à la figure suivante.
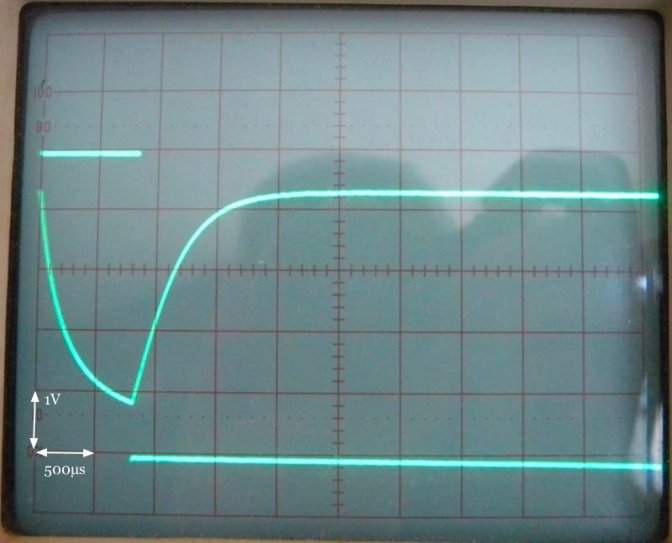
Pendant ces mesures, j’ai posé, par hasard, ma carte de référence des codes de couleur de résistances sur le banc. Il s’agit d’une carte noire mais dont la surface est légèrement glacée. J’ai constaté que la réponse du phototransistor avait changé comme ceci :
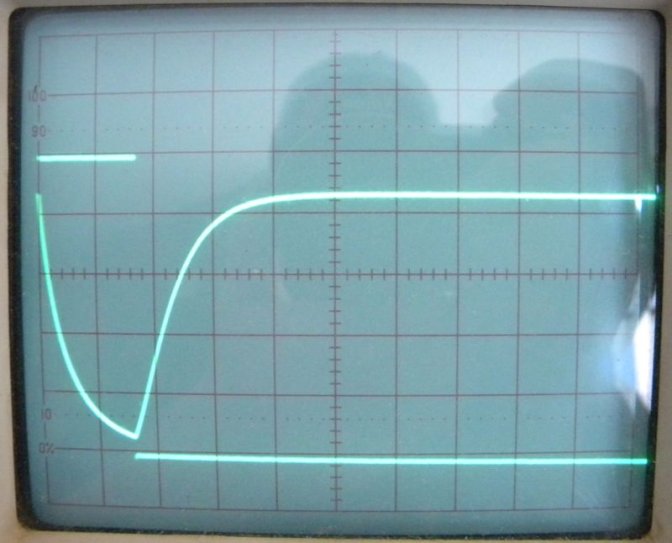
En effet, la carte glacée agit comme un réflecteur et le phototransistor voit le faisceau direct de la LED mais aussi son image sur la surface réflechissante et par conséquent reçoit une intensité lumineuse plus importante.
J’ai réalisé que mon banc était assez éloigné de ce que serait le TCO. Le TCO aura un fond noir recouvert d’une surface transparente. De plus, le faisceau IR direct sera plus proche de la surface et le faisceau réfléchi aura un angle d’incidence plus important [1] et correspondra donc à un angle d’émission où l’intensité lumineuse de la LED est plus importante.
J’ai donc entrepris de rapprocher la conception de mon banc de ce que serait le TCO. J’ai rehaussé le « fond » du banc d’essai de 3mm avec une feuille de Depron puis j’ai ajouté par dessus une bande de Canson noir et enfin une bande de verre synthétique d’épaisseur 1,2mm.
Le résultat est spectaculaire. Le phototransistor recevant plus de lumière de la part de la LED IR, sa réponse est beaucoup plus rapide et le niveau bas descend à 0,2V. Pourtant la résistance de tirage a été diminuée à 22kΩ, ce qui explique le meilleur niveau haut.
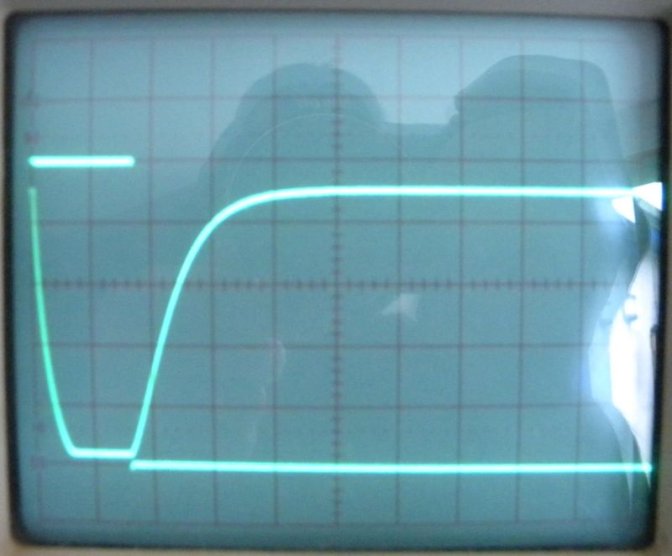
Il reste à mettre en place la dernière amélioration. Le tube d’aluminium au fond duquel était logé le phototransistor n’est pas idéal. Il réfléchit le bruit IR ambiant et fait que le phototransistor conduit un peu en permanence. Le tube d’aluminium est donc remplacé par un assemblage de deux tubes en plastique Evergreen [2] peint en noir à l’intérieur et à l’extérieur par trempage.
Avec cette dernière modification, le niveau haut devient aussi bon que le niveau bas
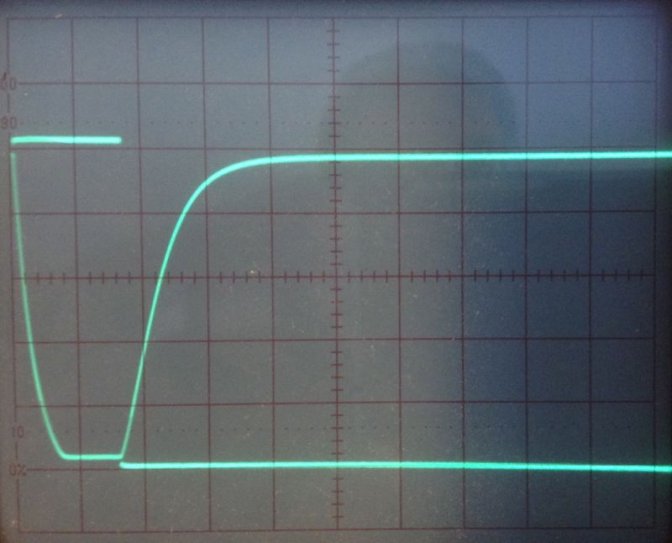
Pour parfaire les essais il reste à vérifier que le phototransistor réagit faiblement à l’éclairage de la pièce comme par exemple la lampe de travail
Ce que permet de vérifier que le tube peint en noir remplit son office même avec un éclairage ambiant à proximité.